HCMC – Given digital transformation taking place in every industry on a global scale, nearly 50% of all processes in the manufacturing sector will need to change in the next three-to-five years as the industry transitions to become fully digital, according to research recently released by ManpowerGroup and MxD USA.
The research, “The Future Factory: Mapping The Skills That Will Power Manufacturing”, describes the impact of digital transformation on the manufacturing sector and highlights the roles of innovation culture and other leadership skills to the business transformation success.
As the vanguard of digital transformation, the industry’s transition to complete digitization is already well underway and accelerating daily. In tandem with that process, new roles demanding advanced digital skills appear, while others become obsolete.
Since its inception, the manufacturing sector has undergone and evolved through four technical generations – Generations Zero to Three, with each generation having different eras of manufacturing tools, technologies and work. Experts said the sector was fully immersed in Gen Three in 2020, characterized by the transformational power of radical improvements in connected systems and machine learning.
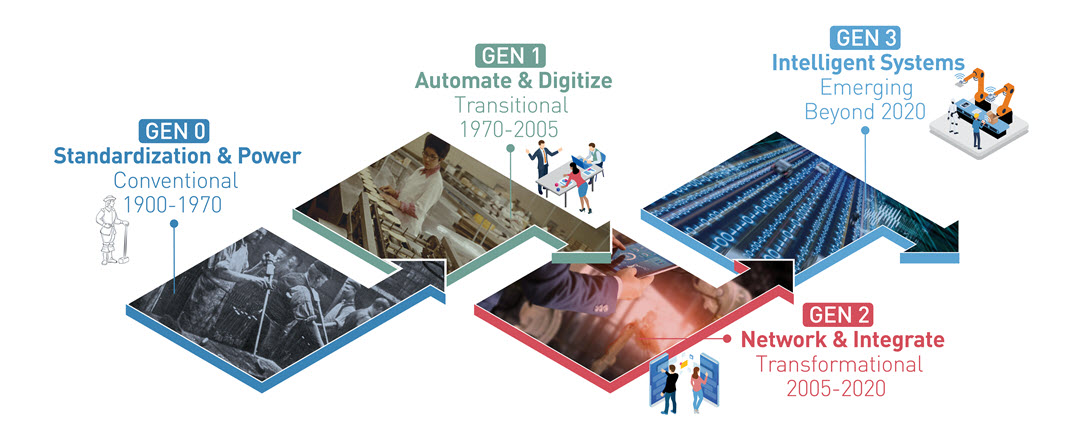
The workforce analysis identifies 165 new roles across seven areas of technical expertise in manufacturing—Digital Manufacturing, Digital Thread, Digital Enterprise, Digital Product, Digital Design, Supply Network and Omni. The impact of transformation differs for each domain with the greatest shift occurring in Digital Manufacturing – 28% of the 165 new roles are in this domain.
“To develop talent, they need to remain competitive; manufacturing companies need new approaches for training, to upskill and reskill people at speed and at scale. It is now or never,” said Le Thi Kim, Head of Staffing and Outsourcing Services, North, ManpowerGroup Vietnam.
From the researchers’ findings, the most effective skills development and retention are achieved through certification programs of six months or less or on-the-job training.
The technological transformation of manufacturing also proposes a need for leadership roles to change. Managers and leaders should follow the 80/20 rule to stay relevant and competitive. While foundational leadership skills keep playing an integral part, effective leaders must also nurture the additional 20%– an innovation culture and risk management, learnability, adaptability and optimizing opportunities.
The key to catching the shift in digital transformation and skills revolution in manufacturing is a connected workforce strategy at the earliest. Apart from investing in internal talent via development programs and helping people transition to new roles, when necessary, employers should cultivate and connect communities of talent beyond the organization, especially going to the labor market or workforce solutions providers to attract the talent that cannot be built in-house.
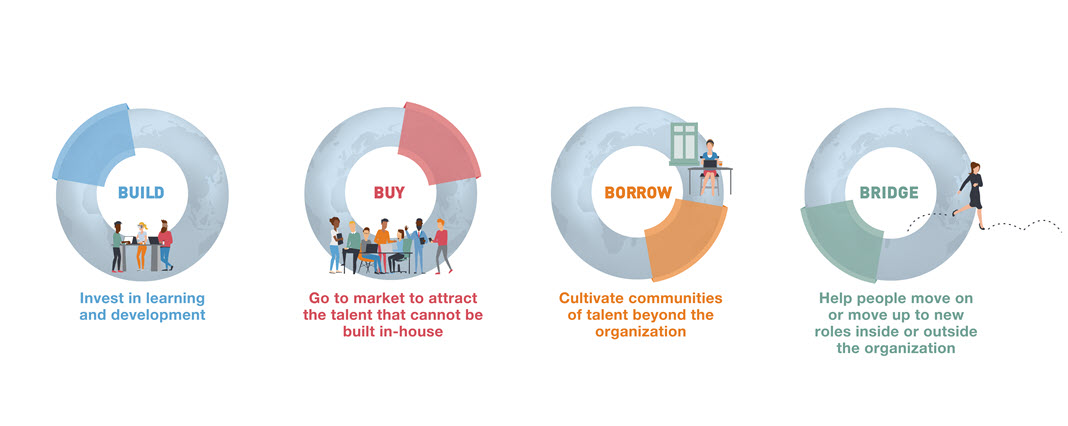